Why plastic extrusion is ideal for mass production
Why plastic extrusion is ideal for mass production
Blog Article
Discovering the Different Methods and Technologies Behind Plastic Extrusion
The world of plastic extrusion is a blend of technology, development, and accuracy, crucial to various industries worldwide. Advanced equipment, electronic controls, and a selection of materials assemble in this complex process, producing top quality, long lasting items.
Comprehending the Essentials of Plastic Extrusion
The process of plastic extrusion, usually hailed as a cornerstone in the world of manufacturing, forms the bedrock of this conversation. In essence, plastic extrusion is a high-volume production procedure in which raw plastic product is melted and created into a constant account. The process begins with feeding plastic materials, usually in the kind of pellets, right into a heated barrel.
The Function of Various Products in Plastic Extrusion
While plastic extrusion is a frequently utilized strategy in manufacturing, the products used in this process substantially affect its last outcome. Various types of plastics, such as abdominal, polyethylene, and pvc, each provide distinct buildings to the end product. Producers need to thoroughly consider the residential properties of the material to maximize the extrusion process.
Methods Utilized in the Plastic Extrusion Process
The plastic extrusion process includes various techniques that are vital to its procedure and effectiveness (plastic extrusion). The conversation will begin with a simplified explanation of the essentials of plastic extrusion. This will certainly be adhered to by a breakdown of the procedure in detail and an expedition of methods to boost the effectiveness of the extrusion technique

Understanding Plastic Extrusion Essentials
In the realm of manufacturing, plastic extrusion stands as an essential procedure, important in the production of a plethora of day-to-day things. At its core, plastic extrusion includes changing raw plastic material right into a continuous profiled shape. This is attained by thawing the plastic, commonly in the kind of granules or pellets, and requiring it with a shaped die. The resulting item is a long plastic item, such as a cord, pipeline, or panel finishing, that preserves the shape of the die. This cost-efficient method is extremely flexible, able to create intricate forms and accommodate a wide array of plastic materials. Basic understanding of these fundamentals enables additional expedition of the a lot more elaborate facets of plastic extrusion.
Thorough Extrusion Process Failure
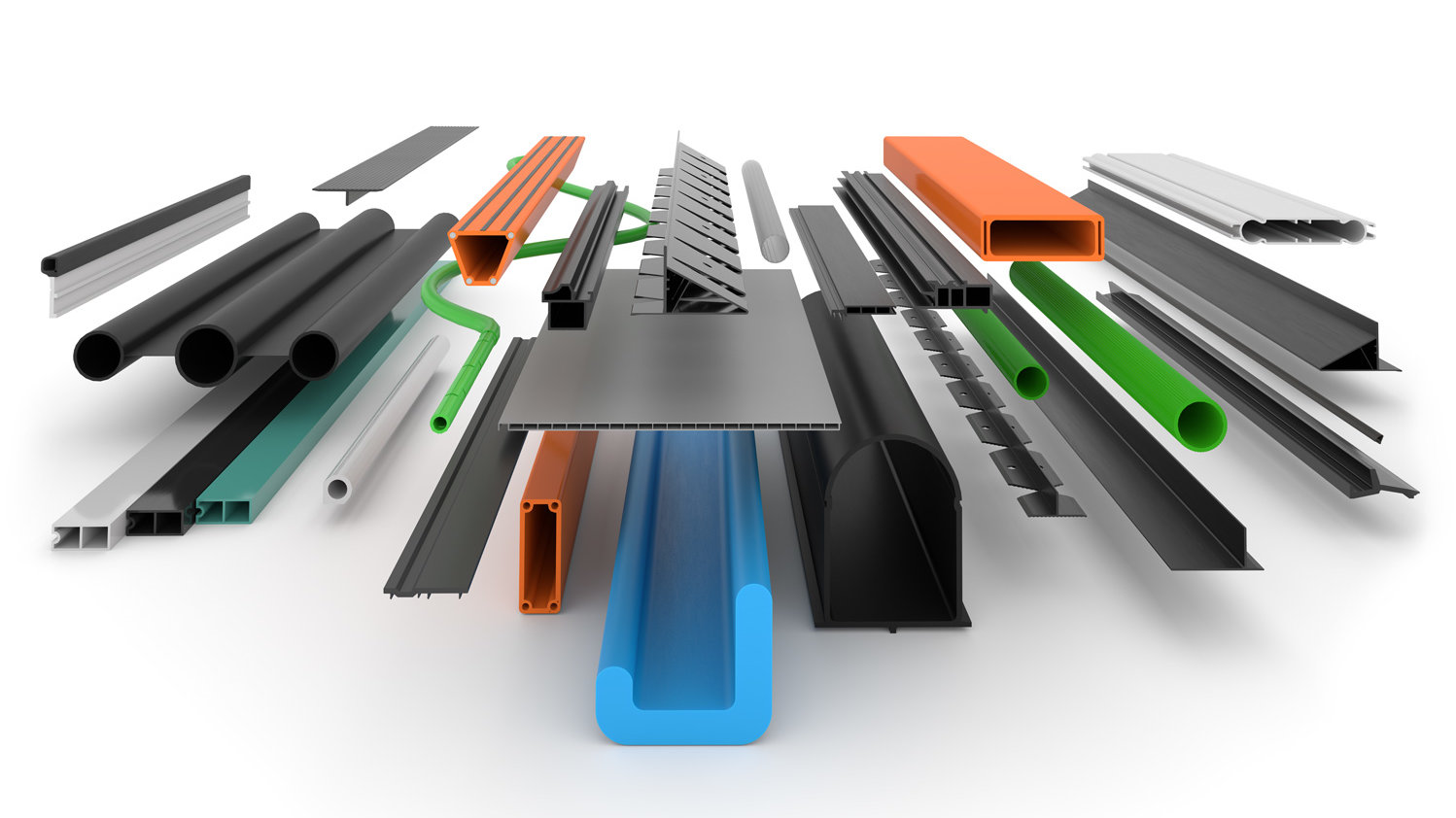
Improving Extrusion Technique Effectiveness
Effectiveness gains in the plastic extrusion procedure can considerably impact both the top quality of the end product and the overall performance of the operation. Constant optimization of the extrusion strategy is vital to maintaining an one-upmanship. Methods that improve performance typically entail precise control of temperature reference level and stress throughout the procedure. Modern modern technologies, such as electronic systems and sensing units, have contributed in attaining this control. The usage of high-quality raw materials can lower waste and boost result top quality. Normal maintenance of extrusion equipment can additionally decrease downtimes, thus enhancing efficiency. Finally, taking on lean manufacturing principles can help get rid of unneeded steps in the procedure, promoting efficiency gains.
Just How Innovation Is Changing the Face of Plastic Extrusion
The advent of brand-new technology has actually significantly changed the landscape of plastic extrusion. It has led to the development of advanced extrusion machinery, which has actually improved the performance and quality of the plastic extrusion procedure. Advancements in the extrusion process have also been driven by technical advancements, providing improved capacities and versatility.
Advanced Extrusion Machinery
Revolutionizing the world of plastic extrusion, progressed equipment imbued with advanced innovation is introducing a brand-new period of performance and accuracy. These devices, furnished sites with cutting-edge features like automatic temperature control systems, ensure ideal conditions for plastic processing, consequently reducing waste and enhancing item quality. High-speed extruders, for instance, amplify result rates, while twin-screw extruders supply exceptional blending capacities, crucial for developing complicated plastic blends. Furthermore, digital control systems offer unmatched accuracy in procedures, minimizing human error. These equipments are made for longevity, reducing downtime and upkeep costs. While these developments are currently remarkable, the constant advancement of modern technology assures also better jumps ahead in the field of plastic extrusion equipment.
Innovations in Extrusion Procedures
Using the power of modern-day innovation, plastic extrusion procedures are undergoing a transformative metamorphosis. With the introduction of 3D printing, the plastic extrusion landscape is additionally increasing right into brand-new realms of possibility. These technological advancements are not only improving the high quality of extruded plastic items however likewise propelling the market towards an extra lasting, efficient, and cutting-edge future.
Real-World Applications of Plastic Extrusion
Plastic extrusion, a versatile and effective process, finds use in many real-world applications. The vehicle market also uses this technology to produce components like plastic and trim bed linen. The stamina and adaptability of plastic extrusion, paired with its cost-effectiveness, make it a vital process throughout various markets, underscoring its prevalent useful applications.
The Future of Plastic Extrusion: Trends and predictions
As we look to the perspective, it becomes clear that plastic extrusion is poised for substantial developments and improvement. Environment-friendly options to traditional plastic, such as bioplastics, are additionally expected to gain grip. These patterns show a dynamic, progressing future for plastic extrusion, driven by technical innovation and a dedication to sustainability.
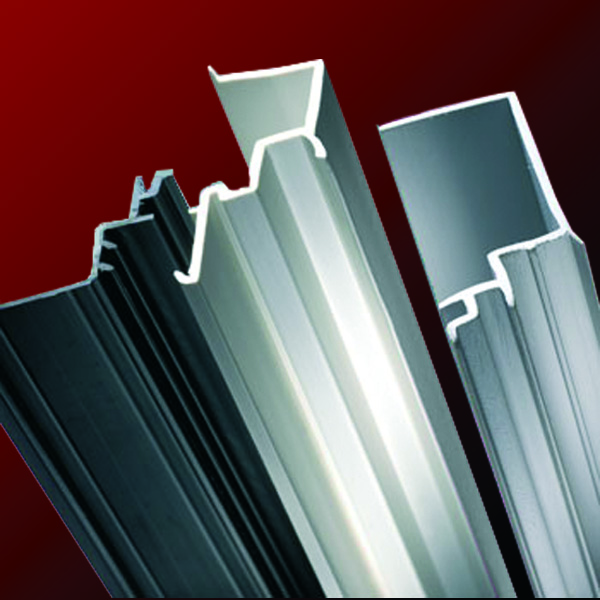
Conclusion
To conclude, plastic extrusion is an intricate process that makes use of advanced technology and varied products to create diverse products. Technical developments, such as digital controls, enhance the production process and guarantee constant outcomes. Additionally, the sector's focus on sustainability and smart machinery suggests an encouraging future. As plastic production remains to advance, it continues to be a vital part of several industries worldwide. look what i found
In essence, plastic extrusion is a high-volume production process in which raw plastic material is melted and developed into a constant account.While plastic extrusion is a commonly utilized technique in production, the products made use of in this process significantly affect its last outcome. At its core, plastic extrusion includes changing raw plastic material right into a continual profiled shape. It has led to the growth of sophisticated extrusion machinery, which has actually improved the performance and high quality of the plastic extrusion procedure.In final thought, plastic extrusion is a complex process that makes use of advanced modern technology and varied materials to create diverse items.
Report this page